|
Friday 1st June 2007
Over the last few weeks I have been collecting suitable items for
Hog 3. Some have been old items that I aquired whilst building Hog 1 and 2,
while others I have bought specifically for the new Hog.
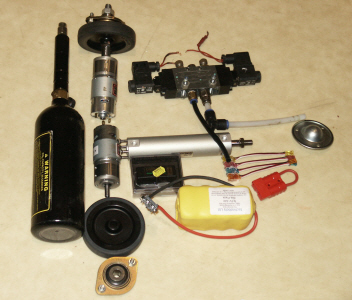 |
The main items are a paint ball bottle with regulator (far
left), 2 drill motors, trolley wheels and bearings, (left centre), one ram, 5/3
valve, receiver, and NiCad batteries, (centre), and one safety link and roller
ball (right).
I had done some intial research before buying the drill
motors and NiCads from technobots, so these should be roughly the right size. I
had also used my flipper
calculator spreadsheet to work out how big the ram needed to be that I
would use to flip a 12kg weight, based on the pneumatics running at 10 bar
pressure. |
One of the first things I decided to tackle was how to fit
the trolley wheels to the motor shafts. The drill motors had a 4 to 1 gearbox
fitted to them, so I would be able to fix the trolley wheels directly to the
motor without any further gearing in between. I knew I had to make some kind of
shaft to fit the wheel to, but there were a couple of problems that I had to
overcome first. The first was how I was going to lock the trolley wheel to this
shaft, and the second was how I was going to lock the motor spindle to this
shaft too.
|
The latter appeared to have an easier solution because
the motor spindle had a flat machined on it. The trolley wheel, on the other
hand, had only a simple hole machined throught it which was going to pose a
more difficult problem. Trolley wheels are usually meant to spin on the axle,
so there was no obvious way of locking the axle to the shaft, but after some
thought I came up with a solution that would solve both problems in one go.
|
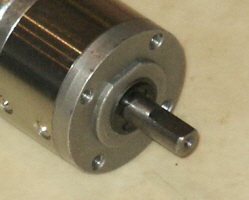 |
|
|
I found an old swinging arm bolt lying around the garage
that was going to be ideal as the source material for the axle. I had recenly
inherited a small lathe from my father, so would be able to turn this bolt down
to the correct size myself rather that give the task to an outside
company. |
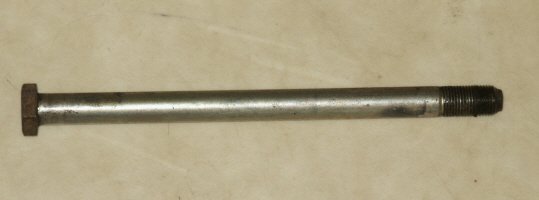 |
After the first phase of machining, the shaft was cut to
length and had the right hand section machined with a hole that would
accommodate the motor spindle. The middle section was machined to fit the
trolley wheel and then the plummer bearing, while the left hand section was
threaded so that a bolt could hold the bearing and trolley wheel in place
together. |
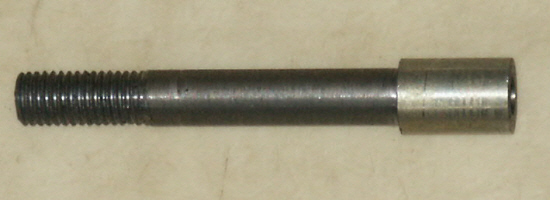 |
The next stage was to file a flat on the motor spindle
section of the shaft. It was filed down to the level of the flat on the motor
shaft so that a flat peice of metal could then be welded in place, therby
locking the motor spindle to the wheel shaft |
|
Here you can see the flat metal plate after it has been
welded in place, and machined back to the profile of the shaft. I had tapped a
thread in the middle of this plate and fitted a grub screw that would hold this
shaft in place on the motor spindle.
The plate not only covered the motor spindle section, but
was extended a couple of millimeters into the trolley wheel section of the
shaft. In this way it could locate onto the trolley wheel an lock it onto the
shaft. |
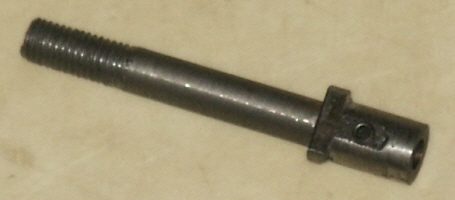 |
You can see below where I cut a flat into the middle part of
the trolley wheel so that the extended plate would fit snuggly against it and
lock all the items together. |
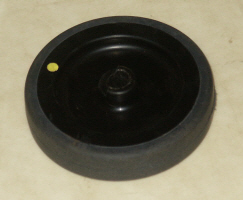 |
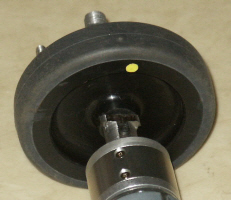 |
Here is the finished item with the plummer bearing, trolley
wheel, and motor all in place on the shaft. |
 |
|
|
|
top |